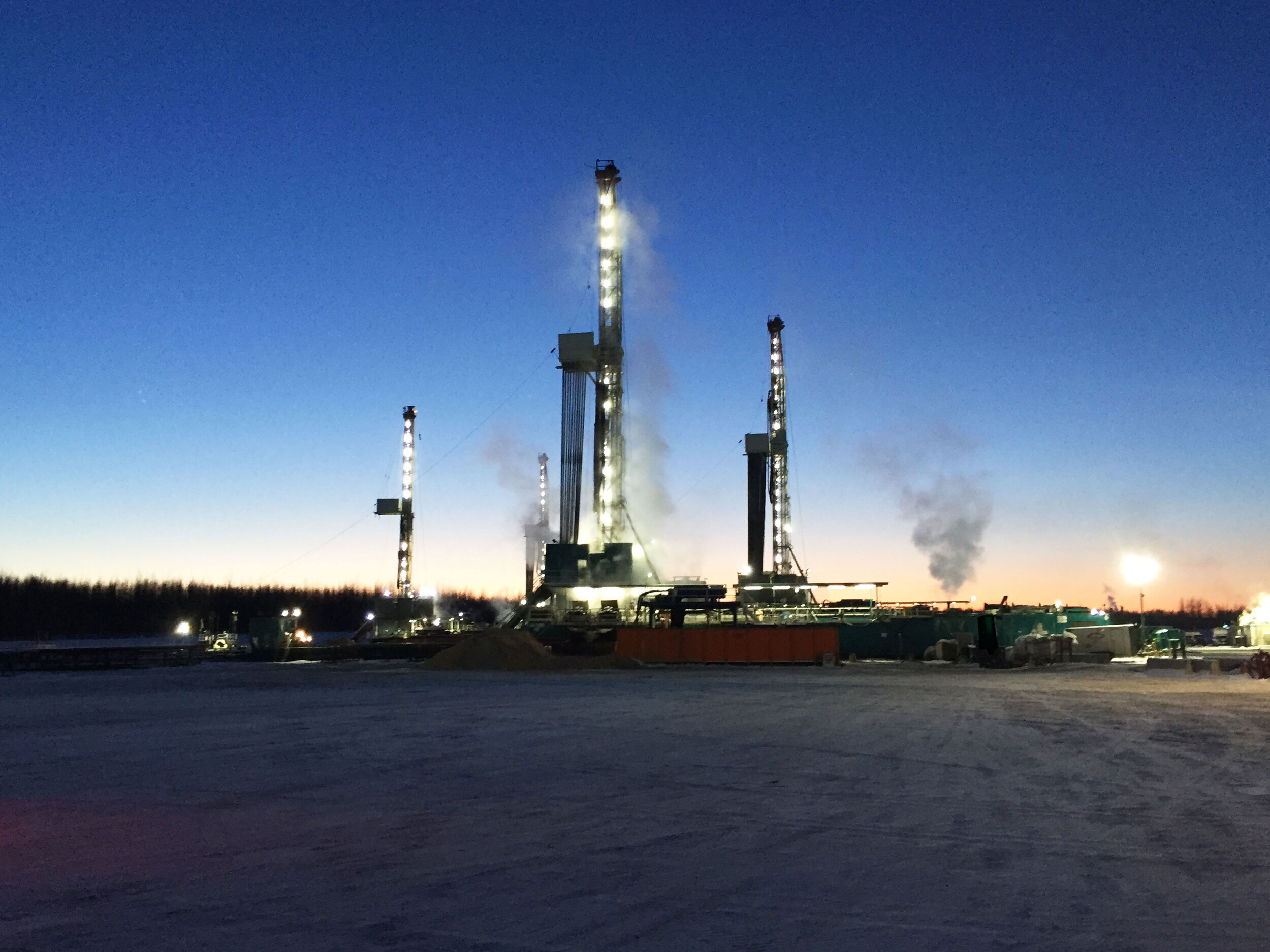
Technology
The patented Disrupter® exploits the negative energy of hole drag by turning side contact force into applied casing oscillation.
How It Works
When traversing the casing string, the moment side contact force is applied on the Disrupter® in deviated conditions, the patented blade design engages the wall of the wellbore and rotation is initiated. In its rotating state, the Disrupter® oscillates, which in turn applies that same oscillation motion on the casing string. Effectively turning sliding friction into dynamic friction. And the rotation frequency of the Disrupter® is solely controlled by the run speed of the casing.
The Benefit
The Disrupter® reduces friction factors by turning sliding friction into dynamic friction, reduces casing run time, and increases available hook load at TD to plan for extending the lateral sections to maximize reservoir exposure. The Disrupter® requires no engineering changes to implement in your existing well design, it is formation independent, completion type independent, and mud type independent.
Trusted
Delivering reliable performance. Since commercializing our first product in Q3 2019, our satisfied clients have run over 300,000 Disrupter® centralizers
Manufacturing The Material
Our staple manufacturing process involves injection molding the Disrupter® with a proprietary resin product that has superior impact, wear, and heat resistance. We rigorously bench test each size of the Disrupter® on a certified API hydraulic press with the Disrupter® heated to replicate downhole temperatures, all tests are conducted with the Disrupter® installed on casing and floating up against the casing coupling to simulate downhole conditions.
If high bottom hole temperatures are in your drilling program, take comfort that our Resin Disrupter® has successfully been run in lateral geothermal applications.
We are not limited to resin, machining the Disrupter® out of alloy, and non-magnetic alloys is something we have done, and currently do.
Future Innovation
What’s next? Clients have realized the operational value and increased profitability with the casing running performance of the Disrupter®, and thus have approached us to design a solution for a complex issue common to the industry worldwide. Challenge accepted. We are accelerating the design of the next Disrupter® product line, initially a tailored one-off for first deployment, followed by scaled commercialization.
IP
The Disrupter® is an industry first with IP awarded in multiple countries, and we are not stopping there…
Proof of Concept Trials
Oklahoma, USA
Trials were completed at a 3rd party Oklahoma test facility.
A 3rd party was contracted to supply the MWD equipment used to capture radial and axial shock & vibration and provide post run analysis.
The subject test well had an open hole section from 0° inclination through to a lateral section with 88° inclination.
The first BHA assembly was a slick string run to TD to capture the drill string radial and axial shock & vibration. This trip to TD set the baseline benchmark for data analysis.
Two trips were made to TD with the Disrupter®.
Right from the kick-off point, with applied side contact force, the Disrupter® rotation was confirmed by captured radial shock readings.
As displayed on the chart to the right, the radial shock spikes represent the Disrupter® rotating off the high side blades.
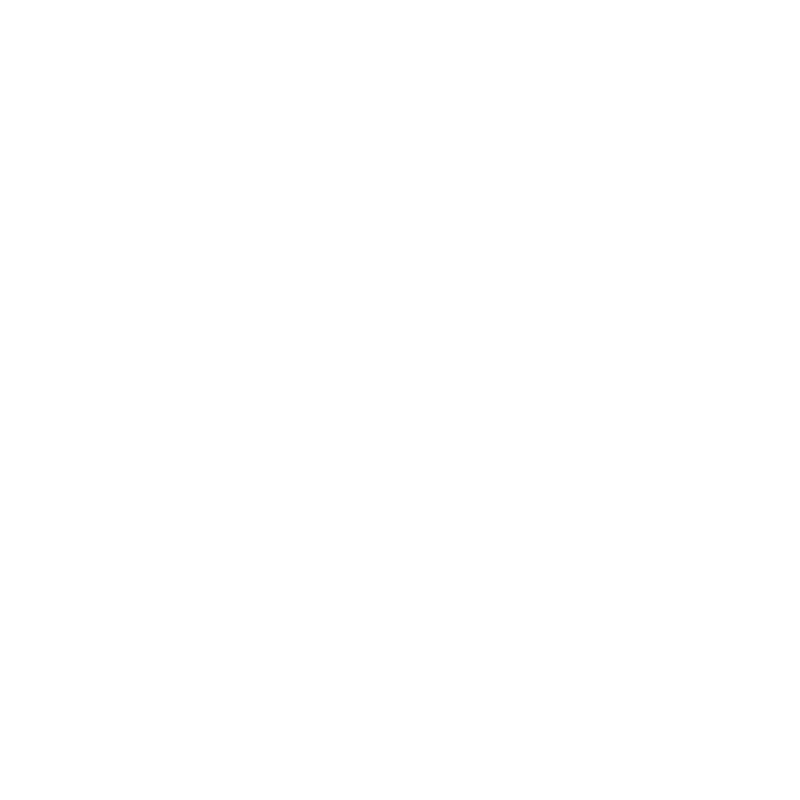

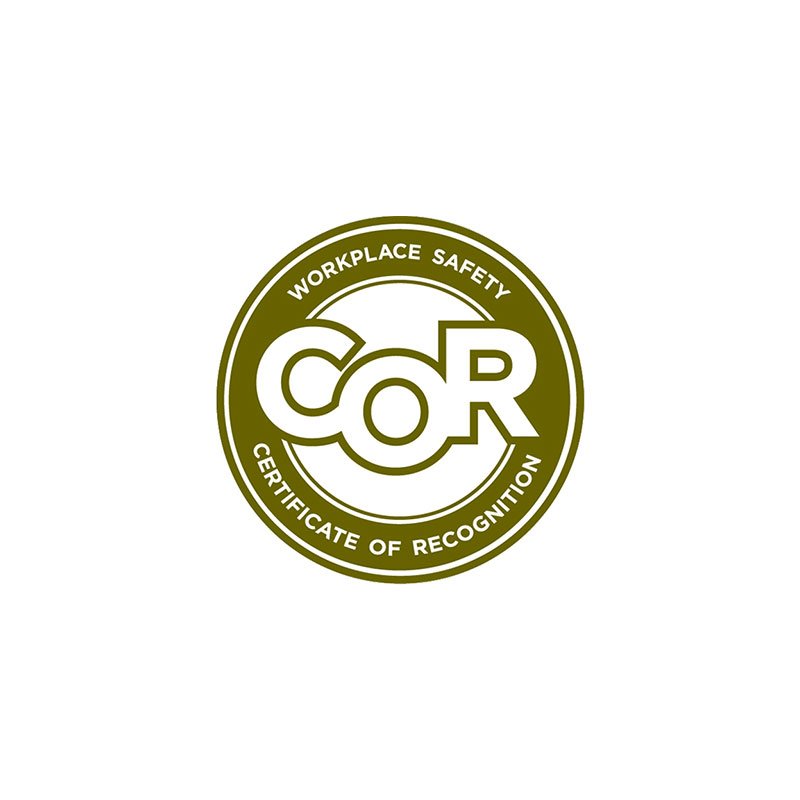
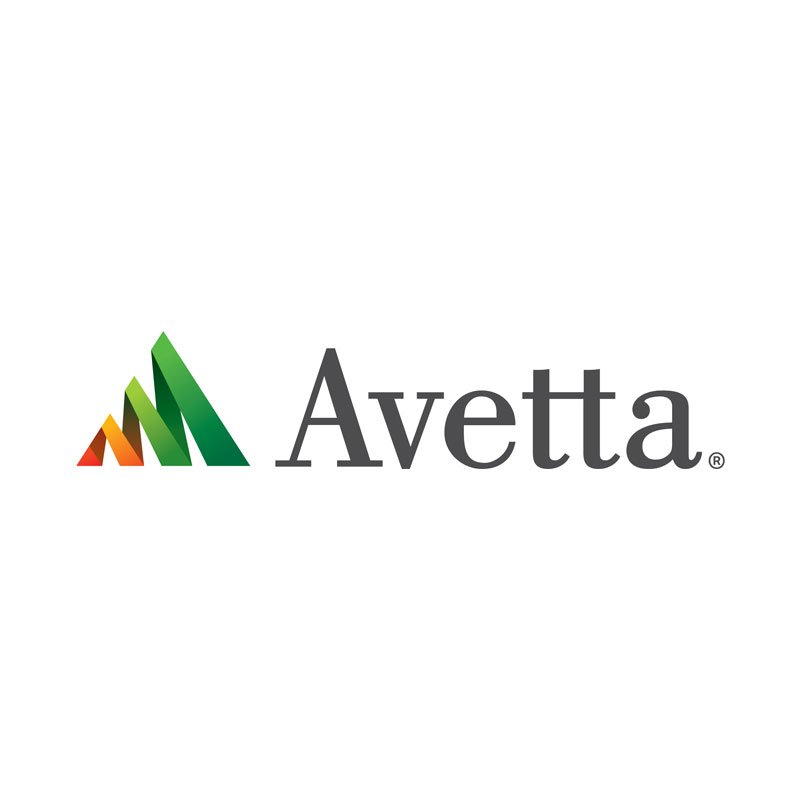
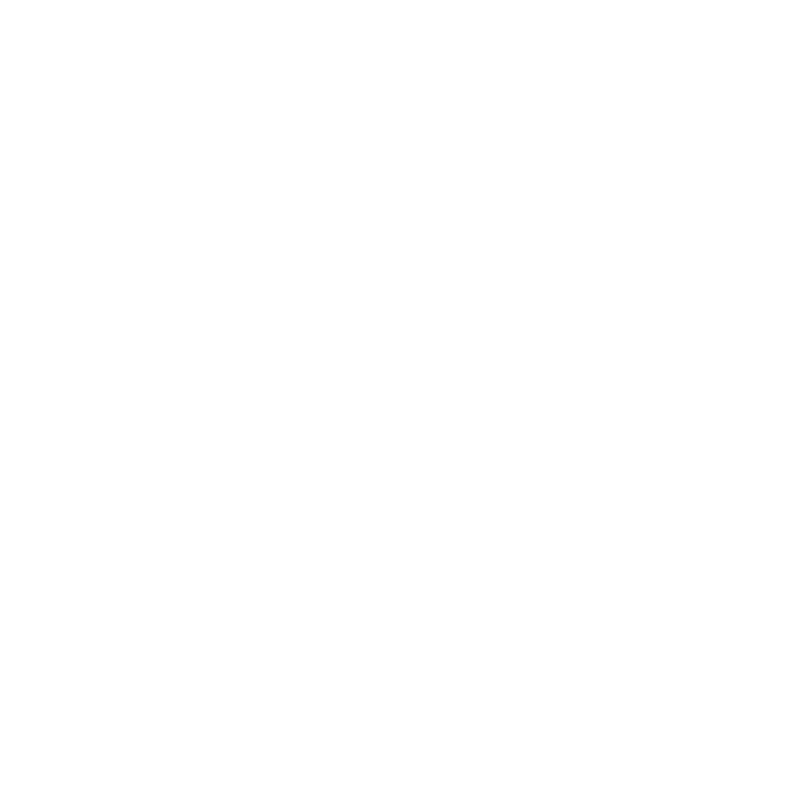